The Value of Traceable Manufacturing in the Context of Global Sourcing
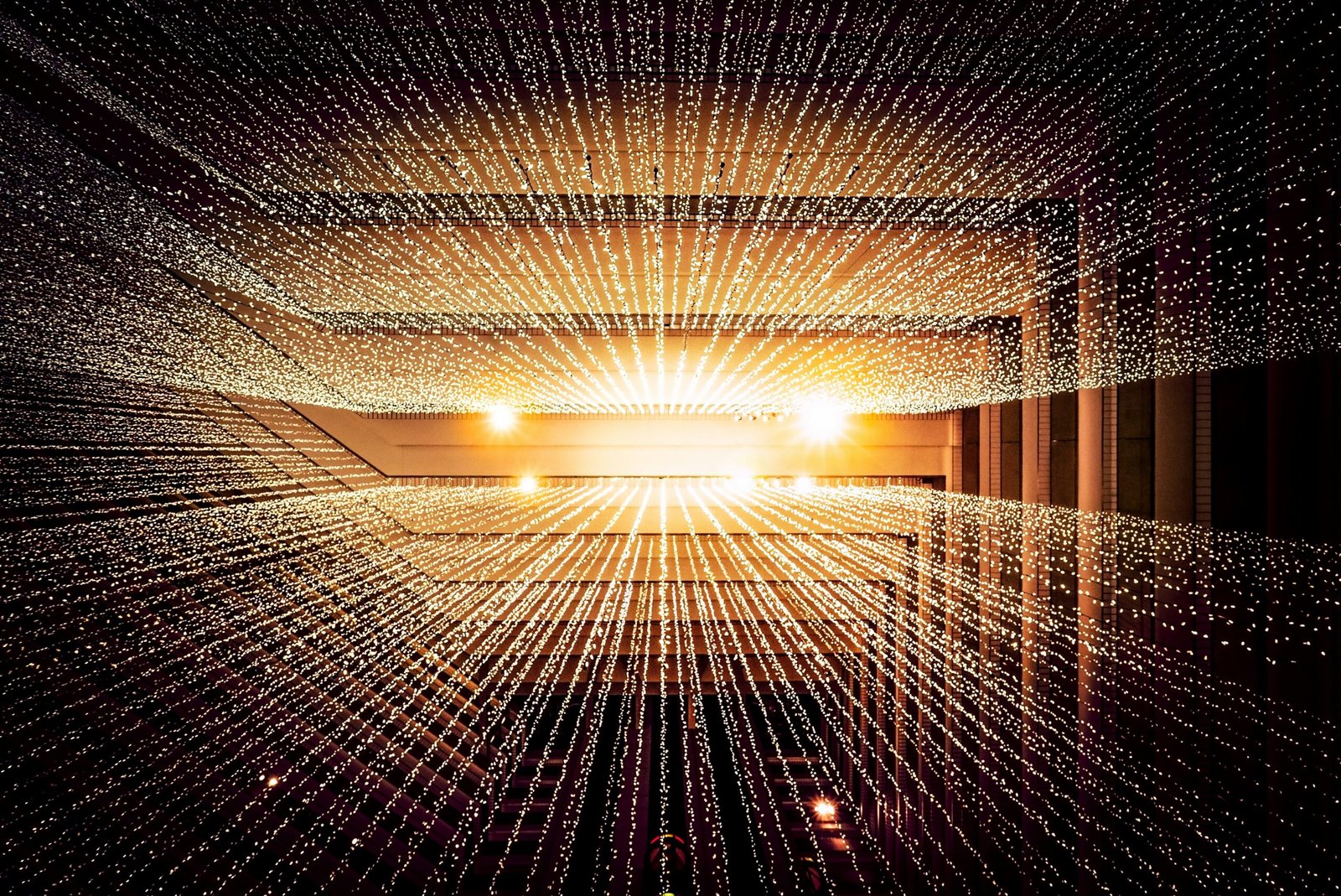
You’ve probably noticed escalating issues. The Value of Traceable manufacturing ensures quality. It meets compliance and provides transparency. This builds trust with consumers and stakeholders if you’re reading this. These issues include uncooperative distribution partners and poor downstream inventory management. You also see problems like fake products and product piracy that have occurred during the past two years. These problems have been exacerbated by supply chain shocks. They are brought on by the pandemic, natural catastrophes, skyrocketing oil costs, political unrest, and conflict. These factors pose extra difficulties for your brand and business.
We have gathered key insights from our implementation of product traceability technology. These insights are based on our work across complicated global supply chains for businesses like ExxonMobil, Dupont, and Rémy Cointreau. We responded to the gap between the demand for high-quality information on traceability solutions and the lack of quality information.
Who is this intended for?
You hold a leadership position at a large industrial or packaged products firm. This is also at an international assistance organization. Your role involves marketing, distributor management, and supply chain management. It also includes printing and packaging, digital transformation, and innovation.
How does product traceability work?
The capacity to follow and trace items through your supply chain is crucial. This process starts from the point of production or manufacture and continues to the final consumer. It is referred to as product traceability. Product traceability, which is used to improve supply chain visibility, necessitates the creation and management of supply chain data.
Businesses today can gain from modern traceability technologies in the following ways:
- Finding and identifying the origins of parallel imports and product diversion
- Creating visibility for distributor and channel channels and determining the product’s path to market
- Developing tools for inventory planning and demand forecasting
- Supporting environmental initiatives including carbon footprint tracking, recycling, and the circular economy
- Monitoring recalled goods, returned goods, damaged goods, and faulty goods.
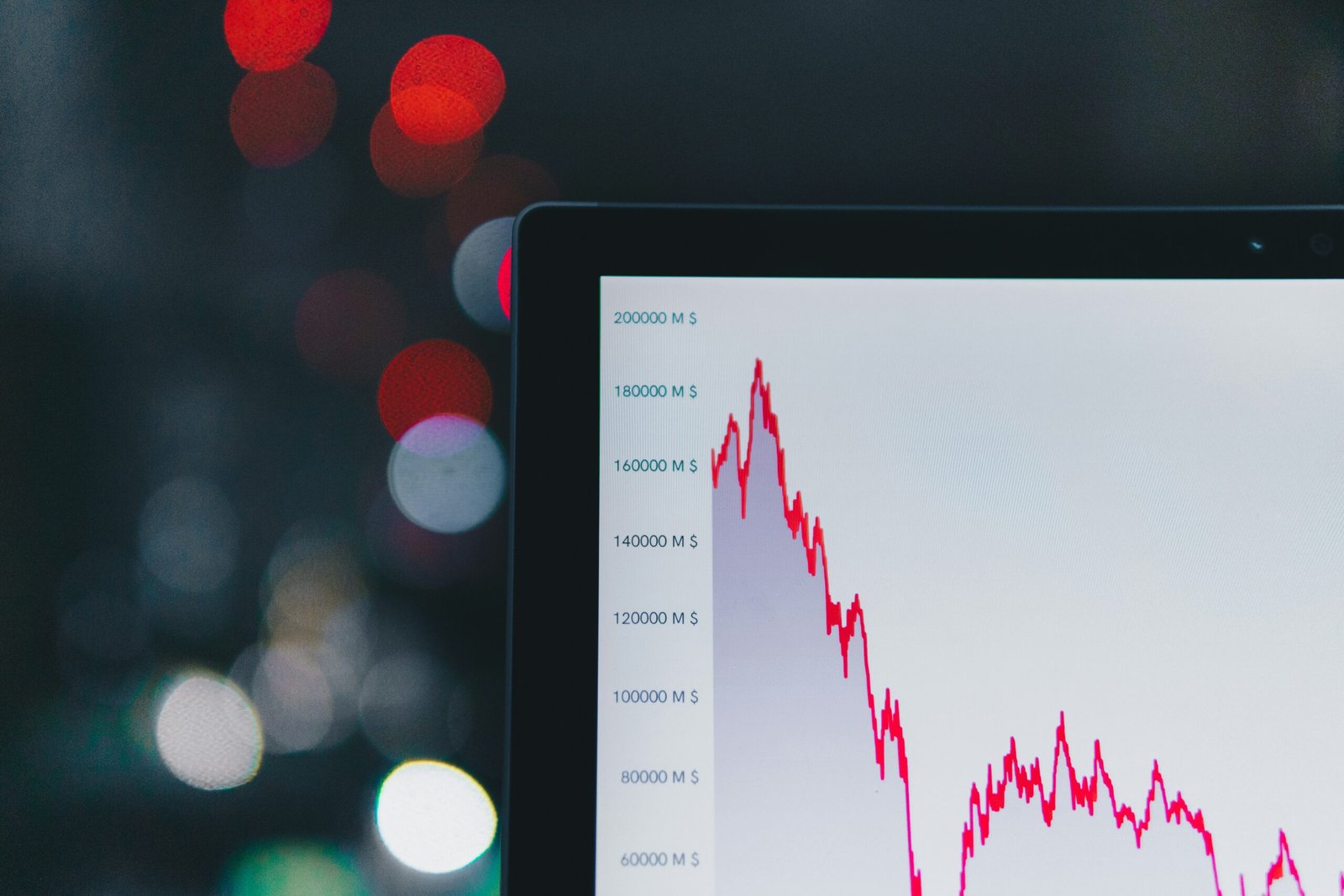
A review of the technology required for product tracing
Although not all are necessary, the technological procedures and technologies are required for traceability:
Integrations with your ERP, Value of Traceable Manufacturing Execution System, and printing systems are necessary. You also need warehousing systems to record all pertinent supply chain events. Your traceability platform is essential at the point of origin.
The difference between upstream and downstream traceability
Traceability along the supply chain is divided into “upstream” and “downstream” traceability. Downstream refers to tracking your product after the Value of Traceable Manufacturing through the supply chain to the client. Upstream refers to the origin and travel of your product’s inputs, ingredients, or raw materials.
Advantages of product and supply chain visibility and traceability
- By identifying parallel imports, enhancing distributor inventory management, and streamlining product recalls, traceability offers significant value. It assists with regulatory compliance and aids in achieving sustainability goals. It also informs end users of the product’s origin. These benefits are especially important for businesses with complex supply chains and distribution networks.
- Demand forecasting, distributor inventory management, sales, and operations planning, and supply and demand management (S&OP)
There are two sorts of advantages that product traceability can offer for distributor inventory management and demand forecasting:
- Visibility into the activities of distribution centers can help forecast demand. It can enhance downstream inventory management. It aids sales and operational planning. This is particularly significant for goods that are prone to promotions or seasonality. Fewer shortages or overstock and better cash flow management are the benefits of improved demand management.
- Knowing the kind and quantity of inventory at distribution hubs helps brands. They can find outdated items. These items should be rushed to market and replaced with more modern ones.
Track product recalls, returns, broken goods, flaws, and warranty claims
- Items that have been recalled can be located using traceability systems. These systems can also follow the products through their distribution chain. They trace the products farther upstream to their manufacture and processing.
- The distribution and shipping information for each product is provided by unit-level tags on current traceability systems. This information includes the Value of Traceable Manufacturing data, like batch and lot details. It also covers logistics or shipping data. This includes box, crate, and pallet information from various points in the supply chain. With this information, businesses can spot distributional problems. These problems affect the quality of their products. This, in turn, impacts their profit margins.
Compliance with laws and trade restrictions
Many sectors are governed by laws requiring goods to be traceable to the unit level. These laws include requirements for their components, raw materials, and other inputs. Only serialization can achieve this at a fair cost. This involves printing, labeling, or even laser stamping special codes on goods and packaging.
Data on downstream product traceability: “Where has your product gone?”
Downstream traceability data, as opposed to upstream data, originates at the place of production and continues along the supply chain. The product’s maker or manufacturer, distributors, and customers produce it. They scan the part’s packaging, product, or the product itself.
The devices can cost up to USD 100, and monthly international data rates apply. Businesses use them more often for high-value goods. Companies also use them for higher-level logistical units like cargo containers. Additionally, they use them for a very limited piece of the supply chain that is under close examination. Businesses can build a unit-collection mechanism after each trip to make implementation cost-effective.
The benefits of using specific, purpose-built traceability software include:
- Integrates multiple MES and ERP systems from internal and third-party supply chain partners. Combines them into a single source of truth.
- Adapts to the demands of various corporate users. These include supply chain managers, demand and inventory management, channel managers, marketing, brand protection, and executives. They can securely login with the appropriate access. Users can access analytics and tools for their traceability use case.
- Allows for the easy building of mobile web pages. These pages be used to show product information. This information can include details about the product’s origin or supply chain. It is useful to end users or professionals.
- Have fewer first and continuing expenditures than internal ERP system development, customization, or expansion.
Which “Layer” does a product traceability system belong to in the ISA 95 Framework?
In the Layer Model for Technology and Business Processes in Value of Traceable Manufacturing, the ISA 95 Framework developed a classification. In this model, end-to-end product traceability systems are Layer 5 solutions. ERP, MES, and other IT systems help them integrate vertically with solutions in layers 0 through 4. They also consume and connect data throughout the supply chain network.
According to the ISA 95 framework (L’s), several components of the traceability technology stack fit into the following categories:
- Physical labor includes assembly. They refer to it as layer 0 through layer 3 solutions in the context of product production. The level 4 solution often receives product data from these levels, which is the next level.
- Experts consider systems like ERPs as layer 4 solutions. They track items from the production and packing stage to delivery. Nonetheless, they do not track items farther down the supply chain among stakeholders.
- The term “Layer 5 solutions” refers to hardware, software, and procedures. They work across distributors and end users. These solutions also work with other supply chain participants at the network level. They connect to the originating ERP to deliver a single source of truth for the entire supply chain.